工場・倉庫の作業動線の改善はどのように行う? 動線を改善する際のチェックポイントも紹介
工場・倉庫の作業動線が適切かという点は、作業の効率性や安全性を確保するうえで非常に重要な要素です。しかし、「自社工場の動線は今のままで問題ないのか?」「問題があるとすれば、どのように改善すればいいのか?」といった疑問を持つ方も多いのではないでしょうか?
そこで本記事では、工場や倉庫の作業動線を改善する際のチェックポイントや、改善を行う際の流れを解説します。
高輝度蓄光テープ-エルクライト™.png)
高輝度蓄光テープ-エルクライト™.png)
工場・倉庫で作業動線の改善が必要な理由とは
工場・倉庫のレイアウトは業務の流れを考慮したものになっていないと、作業者にとって不便かつ危険なものになってしまう可能性があります。
レイアウトが不適切だと、例えば以下のようなリスクがあります。
– 作業者同士が交錯する形の動線になっていることによる、接触事故のリスク
– 人と機械設備が近接した動線になっていることによる、接触事故のリスク
– 動線が必要以上に長いために発生する時間のロス
– 保管と出荷のエリアが明確に区分けされていないことによる、出荷ミス増加のリスク
– 関係部署間の距離が遠い動線になっていることによる、伝達ミスの発生リスク
工場や倉庫の動線をどのように設計するかによって、安全性や効率性は大きく左右されます。
安全・安心な作業環境を整備しつつ生産性を高めたいのであれば、動線改善に取り組むことが不可欠です。
作業動線を改善する際のチェックポイント
自社の動線が適切かどうか確認する際には、以下のポイントを押さえることが重要です。
通路の幅は十分か、安全確保はできているか
工場・倉庫内の通路の幅は、作業員や運搬車両が安全に通行できるように十分なスペースを確保することが必須です。具体的には、労働安全規則によって機械の間または他の設備の間に80cm以上の間隔を空けなければならないと定められています。
最低限の幅を確保することで、緊急時の避難や事故時の救助活動がスムーズに行えるようになります。また、通路の両側には障害物がないか確認し、作業環境の安全性を高めることが重要です。加えて、通路面の高さ1.8m以内に障害物を置かないことや、通路面のつまずきや滑りの危険がないようにすることも求められます。
定期的な点検を行い、通路の整備や清掃もこまめに行うようにしましょう。
確保すべき通路幅の詳細については、以下の記事で解説しています。

多くの動線が重なり合っていないか
作業員や機械などの動線が重なり合うと混雑し、作業効率の低下や事故のリスクが高まります。特に、重要な機器や原材料の搬入出が行われるエリアでは、動線の分離が必要です。主要な通路と作業エリアの動線を明確にしつつ、異なる工程間の動線が交差しないよう配置を工夫することが大切です。
動線を明確にするためには、色分けや標識の設置、床面のライン引きなどを行うと良いでしょう。必要に応じて一方通行の通路を配置することも選択肢の1つです。
また動線を見直す際には、業務フローの変更や新たな機器の導入に伴い、定期的な評価を行うことが重要です。
頻繁に使う設備やエリアまでの距離が適切か
頻繁に使用する設備やエリアまでの距離は、作業効率に大きく影響する要素です。設備やエリア間の距離が適切になるよう動線を工夫することにより、作業者の移動時間が短縮し、生産性を向上させることができます。
関連する作業が隣接するように設備を配置することで、効率的な動線を確保できるようにもなります。重量物や大型部品を扱う場所を、搬入・搬出口に近い位置に配置することも効果的です。
変更時には、実際に作業を行う従業員の意見を取り入れるようにしましょう。
生産量の多い商品の動線が不必要に長くないか
生産量の多い商品の動線が必要以上に長いと、運搬作業にかかる時間が長くなり、全体の生産効率が低下します。生産ラインや倉庫、出荷エリアの位置関係を考慮し、原材料や部品の搬入から完成品の出荷まで、一連の流れを踏まえてレイアウトを最適化する必要があります。
また、動線が長くなっている場合には、工程の見直しや設備の再配置を行い、無駄な移動を削減することが重要です。これにより、コスト削減や納期短縮につながり、作業者の負担も軽減できます。
これらの点を考慮しながら、定期的に作業動線の見直しを行うことで工場・倉庫の生産性と安全性を向上させることができます。チェックポイントを満たしていない場合は、なるべく早急に動線改善を行うようにしましょう。
作業動線改善の流れ
ここからは、作業動線を改善する際の流れを解説します。
①:全体のスペース調査
改善対象となる工場・倉庫のレイアウト図を基に、全体の面積を把握します。この段階で重要なのは、デッドスペースの特定・把握です。その際には下記の3点に着目するようにします。
・平面ロス:
モノが占有していない空間のことです。無駄に空いている場所のほか、人やフォークリフトが移動するための通路スペースとして活用できる空間もあります。
・高さロス:
天井までの垂直空間が十分に活用されていない場所のことです。段積みの高さが低かったり、天井と棚の間の空間が空いていたりする場合に生じます。
・山欠けロス:
保管棚のスペースが十分に活用されていないことで生じる空間のことです。荷姿が統一されていないために、保管棚の上部空間が有効に使われていないケースや、棚の中に空間があるケースなどを指します。
②:動線の分析
次に行うことは、現在の作業者やモノの動きの観察、記録です。その際には、モノの種類ごとに業務の流れを書き出し、それをもとにレイアウト上に業務の流れを記載していきます。そうすることで動線の距離を可視化でき、どの工程でムダな動きや非効率な経路が生まれているのかを特定できるようになります。
この段階で、通路の幅は十分か、多くの動線が重なり合っていないかといった前章のポイントを同時に確認しておくと望ましいです。
③:全体の物量を把握
原材料、仕掛品、完成品などの物量を測定し、どの動線を優先的に改善するかを決める際の参考にします。その際には、各工程での入出荷量や保管量などを確認し、優先的に動線を割り振るモノを特定すると効果的です。
④:業務の流れに沿う設備の配列を検討
人やモノの動きを確認し、業務の流れが類似しているグループをなるべく近い位置に配置するよう検討します。
この際、手順②で使用した業務の流れ記載した図を活用すると効率的です。
また、工場・倉庫全体のレイアウトを考慮して、部門ごとに最適なエリアに配置されるよう工夫することも不可欠です。エリアの配置が適切であれば、頻繁にコミュニケーションをとる部門同士の位置を近づけて伝達のコストやミスを減らしたり、外部の人間が訪問する機会の多い部門を入口付近に配置し、セキュリティ上の懸念を解消したりすることができます。
⑤:レイアウトの設計
分析結果をもとに、実際のレイアウト構想を図面に落とし込みます。
この段階では以下の点を押さえておくと良いでしょう。
・出入りの頻度に応じた配置
・同一作業者のエリアの集約
・工程に沿った配置
・重量物や危険物の移動の容易さ
・騒音、振動、埃などの隣接エリアへの影響
これらの要素を考慮しながら、最適なレイアウトを設計します。
⑥:レイアウト変更の実施
設計したレイアウトに基づいて、実際の変更を行います。ここでは以下の手順に従って変更を実施することがおすすめです。
・レイアウト変更のスケジュールを決定
・担当者を選定
・計画通りに進んでいるか、進捗状況を確認
・変更作業を実施
作業動線変更に伴うミス・事故を減らすには
レイアウトの変更が終わったら実際に作業を行い、これまでの課題が解消されているか、また新たな課題が発生していないかをチェックします。
ミスが起きやすいレイアウトになっている、むしろ効率が低下している箇所があるなど、課題が見つかればその都度改善を行うことが重要です。
レイアウトが確定したあとも、変更後の導線に慣れるまではミスや事故が起こる可能性がありますが、その際に動線の視認性を高めておくことで、ミスや事故の発生を防ぐことができます。
動線の視認性を高める方法としては、「照明の設置や採光を行う」「通路を色で区切る」といった方法があります。
通路を色で区切る際には、屋内区画表示用テープの活用がおすすめです。
環境にやさしい屋内区画表示用テープについて詳細はこちら
動線の視認性を高めるには蓄光テープが効果的
動線の視認性を高めるには、通常の屋内区画テープに加えて、蓄光テープを活用するとさらに視認性を高めることができます。
テープを使ってエリアの区画を分けたとしても、採光によって視認性を担保している場合は、夕方になると視認性が低下してしまいます。そうした場合には、蓄光テープのような視認性を高めるアイテムを活用して視認性を担保することが重要です。
蓄光テープは停電時や避難時の安全確保にも有効
蓄光テープは動線変更直後だけでなく、停電時や避難時の安全性を高めるうえでも重要です。
蓄光テープは電気を使用せずに一定時間発光するため、導入することで停電により電力が供給されない場合であっても、危険箇所や避難経路の視認性を高めることができ、停電時に有効な対策となります。
作業動線の視認性向上には高輝度蓄光テープ エルクライト™がおすすめ
作業動線の視認性向上には、日東エルマテリアルの高輝度蓄光テープ エルクライト™がおすすめです。
エルクライト™は、蛍光灯や太陽光などの光を蓄えて、暗闇で発光する事で目印となる防災用途に開発されたテープです。白色LEDの光も吸収するため、工場や倉庫で停電が発生した際も、高い輝度で現場環境の視認性を高めることに役立ちます。
また、階段や障害物の周りに高輝度蓄光テープを貼ることにより、真っ暗な状態でも危険な箇所がわかりやすくなり、安全に行動することができるようになります。
JIS規格(JIS Z9107)で定められた輝度を大幅に上回り、高い耐候性、耐摩耗性、耐薬品性等を有する、耐久性にすぐれた製品です。
エルクライト™にご興味のある方は下記のサービスページもご覧ください。
お役立ち資料
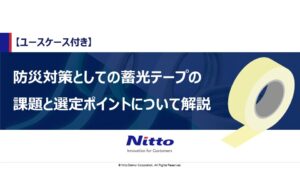
この資料で分かること
- 蓄光テープを効果的な防災対策にするためのポイント
- 防災対策としての”蓄光テープ”の選定ポイント
- 蓄光テープのユースケース(工場・倉庫・建築現場など)
カタログ資料
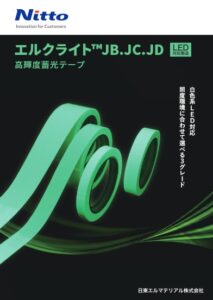