工場・倉庫のヒヤリハットの原因と事例を解説
対策も紹介
工場や倉庫での重大な事故を避けるためには、事故につながりかねない事象である「ヒヤリハット」を防ぐことが重要です。ヒヤリハットを防ぐためには、単に「大きな事故にならなくてよかった」と安心するだけではなく、その原因を把握し、対策をしっかりと講じる必要があります。
本記事では、工場・倉庫におけるヒヤリハットの原因と事例、対策を解説します。
高輝度蓄光テープ-エルクライト™.png)
高輝度蓄光テープ-エルクライト™.png)
ヒヤリハットとは
ヒヤリハットとは、業務中における大きな事故や災害の原因になりかねない出来事のことです。思わず「ヒヤリ」あるいは「ハッ」とするような、一歩間違えれば大事故に至っていたかもしれない状況を指すことからこう呼ばれています。
なお、厚生労働省兵庫労働局は、「危ないことが起こったが、幸いにも災害には至らなかった事象」※と定義しています。業務中に発生したヒヤリハットを記録し対策を講じることで、重大な事故を防ぐことができます。
ハインリッヒの法則
ヒヤリハットに関連するものに「ハインリッヒの法則」があります。これは「1:29:300の法則」とも呼ばれ、「1件の重大な事故の背後には、29件の軽微な事故があり、さらにその背後には300件の事故に至らなかった事象(ヒヤリハット)が潜んでいる」という経験則のことです。
このハインリッヒの法則が知られるようになったことで、重大事故の発生につながりかねない小さな危険要素の芽を摘むことが重要であると認識されるようになりました。
工場・倉庫でヒヤリハットが起こる原因
ヒヤリハットはあらゆる業界・業種で起こり得るものですが、工場・倉庫で起こる原因としては以下の5つが挙げられます。
焦り・油断・気のゆるみ
焦りや油断、気のゆるみは、ヒヤリハットの主要な原因の1つです。特に以下のような状況で発生しやすくなります。
・納期や作業時間に追われて、安全確認を怠る
・慣れた作業による過信から、注意力が低下する
・「自分は大丈夫」という根拠のない思い込み
このように時間的制約や慣れといった要因から、本来確認すべき項目を確認しなかったり、定められた工程や手順を守らなかったりすることがよくあり、その結果ヒヤリハットが起きやすくなります。
疲労
長時間労働や過重な業務により疲労が蓄積すると、注意力や集中力、判断力が低下し、ヒヤリハットが発生しやすくなります。
いつも行っている単純作業でミスが起きたり、通常なら気づくはずの危険な状況を見逃したりすることが多くなるので注意が必要です。
知識・スキル不足
特に新入社員や未経験者において、知識やスキルの不足がヒヤリハットの原因になることがよくあります。
初心者の場合、業務プロセスや作業環境の異常に気づきにくい、何が危険な状態なのかわからないといった状態になりやすいことがその理由です。
情報共有不足
職場内のコミュニケーションが不足している、マニュアルや報告書がきちんと読まれていない、危険情報が十分に伝達されていないなど、情報共有が不足していることもヒヤリハットの原因です。
情報を発信する側はきちんと伝えているつもりでも、受け手側がその内容を正しく理解していないこともあるため、そうした場合には情報共有のあり方を見直す必要があります。
5Sの徹底不足
5S(整理・整頓・清掃・清潔・しつけ)は職場の安全を確保し、働きやすい環境にするために不可欠の活動ですが、5Sの不徹底により作業環境が悪化し、ヒヤリハットを招くことがよくあります。
例えば、不要なものや障害物を整理・整頓していないことよる転倒や衝突のリスク、工具や機材の紛失による作業の遅延や焦り、汚れや埃による機械の誤作動などが考えられます。
5Sの不徹底は、作業効率の低下だけでなく安全性を損なうことにもつながるので、今一度しっかりと行う必要があります。
工場・倉庫でのヒヤリハットの事例
以下では、工場・倉庫でよくあるヒヤリハットの事例をご紹介します。
衝突
倉庫内では、作業者同士が狭い通路や動線を共有することがあり、周囲への注意を怠ることで他の作業者と衝突する可能性が高まります。特に、荷物を運んでいるときは視界が狭くなり荷物に気をとられるため、接触事故が発生しやすいです。
倉庫内では、フォークリフトやハンドトラックなどがよく使用されますが、作業者が周囲の状況に注意を払わない場合、後方から接近するフォークリフトと衝突する危険性があります。フォークリフトの重量は数トンにも達するため、重大な事故につながりかねません。狭い通路や視界が悪い場所では、より一層の注意が必要です。
また、施設内が暗い場合は作業者の視認性が低下するため、作業者同士や施設内の荷物と衝突する危険が高まります。
転倒
床に工具や部品が放置されていると、作業者がそれに気づかず踏んでしまい、足を取られて転倒する危険があります。特に重い荷物を運搬している場合、バランスを崩して転倒するリスクが高く、大きなけがにつながるケースも珍しくありません。また、オイルや水が床にこぼれている状態では、滑って転倒する可能性も高まります。
倉庫内で滑り止めがない不適切な作業靴を履いている場合は特に、滑りやすい床や濡れた場所での転倒リスクが高くなり、大きなけがにつながりやすくなります。また、視認性が低い環境や暗い場所での作業は、滑って転倒するリスクをさらに高めるので一層の注意が必要です。
転倒を防ぐためには、すべり止め効果のあるテープを床面や階段などに貼り付けることも効果的です。
貼るだけで簡単にすべり止め効果が得られるノンスリップテープについて詳細はこちら
墜落・転落
高い棚やラックから物を取る際に、不安定な足場や正しく固定されていないステップを使用すると、バランスを崩し墜落する危険があります。特に安全ベルトを使用していない場合、墜落時に大きなけがを負うリスクが高まります。落下物が他の作業者に当たり二次的な事故が発生する可能性もゼロではありません。
また、倉庫内には階段や高所の通路があり、手すりを使用しなかったり注意を怠ったりすると踏み外して転落する危険があります。荷物を運んでいる際には特にバランスを崩しやすく、転落によるけがのリスクが高くなるため注意が必要です。
切れ・こすれ
倉庫内には鋭利な金属製部品や工具が多く存在し、素手で取り扱うと誤って手や指を切る危険があります。特に部品の隙間に手を入れた際、見えない部分で鋭利なエッジに触れてけがをすることが多いです。
また重い荷物を無理に持ち上げた際に、体に強い摩擦が生じ、腕や手に擦り傷や皮膚損傷が発生することがあります。肌が露出した状態で機械の可動部分に擦れることで、より深刻なけがにつながる場合もあります。
はさまれ・巻きこまれ
フォークリフト作業中に周囲の確認が不十分な場合、荷物とフォークリフトの間に作業者が挟まれる事故が発生することがあります。フォークリフト運転手が後方確認を怠った場合に、近くにいる作業者が挟まれてしまうケースも少なくありません。
また、倉庫内のコンベアを使用中に作業者の衣服や手袋、髪がコンベアに巻き込まれることがあり、非常に危険です。特に機械のメンテナンス時に電源を切らずに作業を行うと、突然機械が動き出し巻き込まれるリスクが高まります。
こうした事故を防ぐアイテムとして、工場や倉庫内の危険表示や注意喚起に使用できるノンスリップシートがあります。
多彩なデザインとすべり止めを兼ね備えた路面標示ノンスリップシートについて詳細はこちら
動作の反動・無理な動作
倉庫では重い荷物を持ち上げことがよくありますが、正しい持ち上げ方をしないと腰や肩に大きな負担がかかり、けがをする可能性があります。特に、膝を使わずに腰だけで荷物を持ち上げようとすると、腰を痛めるリスクが高いです。
荷物の大きさや高さに合わせようとして無理な姿勢をとることもよくありますが、このような姿勢をとると筋肉や関節に不自然な負担をかけ、けがにつながります。急な動作や反動が加わった場合、捻挫や肉離れなどが発生する危険性もあります。
作業に慣れていない新人や未経験者、けがのリスクが高い高齢の作業者は特に注意が必要です。
火災
倉庫内の電気設備や機械が過負荷になり、ショートを引き起こすことで火災が発生する場合があります。電源タップに過剰に機器を接続したり、古い配線を使用したりしている場合、火花が発生しやすく、周囲の可燃物に引火する危険があります。
溶接や切断作業中に生じる火花が紙や布、油などに引火することも、火災が発生する原因の1つです。初期消火が遅れると、火の手が広がり施設全体に被害が及ぶおそれがあります。火が天井や壁に延焼したり、煙が充満し始めたりすると初期消火はほぼ不可能なので、速やかに避難しなければなりません。
工場・倉庫でのヒヤリハットの対策
工場や倉庫でのヒヤリハットを防ぐにはどうすればよいのでしょうか。主な対策をご紹介します。
確認の徹底
ヒヤリハットを防ぐうえで最も基本的かつ重要な対策は、作業開始前に周囲の安全確認や機械・設備の点検を徹底することです。特に、フォークリフトやハンドトラックを使用する際には、運行ルートを確認し、周囲の作業者や機械の動きに注意を払うことで、衝突や事故を未然に防ぐことができます。作業を行う場所の状態や障害物の有無も確認し、危険な場所を特定することも重要です。
荷物を運搬する前には、その重さや形状、運搬方法を確認します。大きな荷物を扱う際には、周囲をしっかり確認して他の作業者との衝突を防ぐために、適切な道具を使用する必要があります。複数人で作業する際は、声かけやハンドサインを使ってお互いの状況確認を徹底することも大切です。
こうした確認作業を日常的に行うことで、潜在的な危険を事前に察知し、事故を未然に防ぐことができます。
体調管理の徹底
作業者の体調不良は、注意力の低下や判断ミスにつながり、ヒヤリハットの原因になるため、体調を定期的にチェックし、健康状態に問題がある場合には作業をさせない、別の者と代わるなどの対応が必要です。作業中に体調が悪化した場合には直ちに作業を中止し、休憩を取る必要があります。
体調管理を徹底するためには、作業時間に応じてこまめに休憩をとったり、長時間労働にならないようシフトを工夫したりする対策が求められます。夏場は水分・塩分補給を徹底し、熱中症を予防することも重要です。
手段・手順の最適化
定期的に作業手順を見直し、効率的で安全な方法に改善することも重要です。その際には以下の点を押さえると良いでしょう。
・作業手順をマニュアル化し、標準化された安全な方法で作業を行う
・危険な作業については、より安全な代替手段を検討する
・作業に適した保護具(手袋、保護メガネなど)を選定し、正しく使用する
例えば、荷物の運搬や高所作業においては、正しい持ち上げ方や移動方法を周知徹底し、誤った方法での作業を防ぎます。また作業内容に応じて適切な機器を使用し、必要な場合はフォークリフトやハンドトラックの利用を促すことで、重い荷物の持ち上げや運搬による負担を軽減できるようになります。
設備・環境の改善
床面の凹凸や工具の放置を防ぐため、定期的な清掃を行い危険物の管理を徹底したり、滑り止めマットの設置や床面のメンテナンスを行い転倒のリスクを軽減したりするなど、作業環境や設備の改善も不可欠です。
倉庫内の整理整頓を徹底し、通路に障害物を置かないようにするとともに、照明を定期的に点検し、十分な明るさを確保することが必須です。
暗い場所や視認性が低い場所では、追加の照明の設置や蓄光テープなどを活用して視認性を確保し、作業や通行に支障が出ないようにすることも重要です。
衝突・転倒のヒヤリハット対策は高輝度蓄光テープ エルクライト™で
工場・倉庫でのヒヤリハットを防ぐためには、日常の確認作業や体調管理、作業手順の最適化など、基本的な対策を徹底することが何よりも大事です。
あわせて、暗い場所での転倒や衝突を避けるため、作業環境の視認性を高める必要があります。
視認性が低い場所の視認性向上には、日東エルマテリアルの高輝度蓄光テープ エルクライト™がおすすめです。
エルクライト™は蛍光灯や太陽光などの光を蓄えて、暗闇で発光する事で目印となる防災用途に開発されたテープです。白色LEDの光も吸収するため、工場や倉庫で停電が発生した際も、高い輝度で現場環境の視認性を高めることに役立ちます。
JIS規格(JIS Z9107)で定められた輝度を大幅に上回り、高い耐候性、耐摩耗性、耐薬品性等を有する、耐久性にすぐれた製品です。
エルクライト™の詳細につきましてはこちらの資料をご覧ください。
お役立ち資料
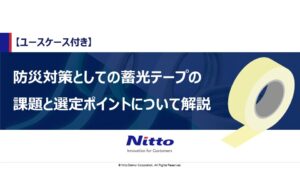
この資料で分かること
- 蓄光テープを効果的な防災対策にするためのポイント
- 防災対策としての”蓄光テープ”の選定ポイント
- 蓄光テープのユースケース(工場・倉庫・建築現場など)
カタログ資料
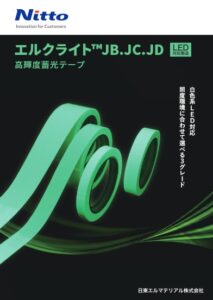